How Mining Companies Benefit from Centrifugal Slurry Pumps
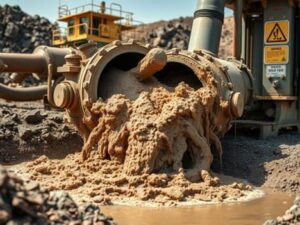
Downtime in mining isn’t just inconvenient—it’s expensive. Every unscheduled pause in fluid transport can delay production targets, increase maintenance costs, and, in the worst cases, compromise worker safety. For operations managers and procurement leads—especially those supporting remote or abrasive environments such as hydraulic fracturing sites—few decisions carry as much weight as selecting the right centrifugal slurry pump technology for slurry-heavy conditions. This article explores how centrifugal slurry pumps meet the unique demands of mining operations, reduce unplanned downtime, and offer long-term ROI in high-solids applications across various rugged environments.
Why Slurry Transport Is a Critical Mining Challenge
Transporting abrasive slurries through fluid systems is a defining challenge in the mining sector. These slurries, often a dense mix of water and finely crushed rock or chemically reactive minerals, create substantial wear on internal pump components. This results in frequent failures, especially in remote or high-intensity sites where operational conditions are harsh and unpredictable.
Pump failures in these environments are not merely technical setbacks. From an operational standpoint, they can disrupt fluid handling processes, lower containment efficiency, and cause environmental compliance concerns—all while increasing total cost of ownership.
Industry observations suggest that mining companies frequently face shortened pump lifespans due to misaligned equipment specs and poorly managed wear rates. Key stakeholders have grown increasingly concerned about how this impacts core KPIs such as mean time between failures (MTBF) and cost per gallon moved.
[ILLUSTRATIVE EXAMPLE]
In a hypothetical scenario, a mining operation situated in a remote region characterized by fracking activity experienced recurring pump shutdowns approximately every six weeks due to abrasive degradation of impellers. After transitioning to a higher-durability centrifugal slurry pump, modeled for aggressive wear resistance, service intervals extended closer to four months. This reduced unplanned maintenance and helped maintain production continuity.
[END EXAMPLE]
What Makes Centrifugal Slurry Pumps Ideal for Harsh Mining Conditions
Centrifugal slurry pumps are engineered with abrasive environments in mind. Unlike other pump types, these systems harness kinetic energy through rotating impellers, converting it into hydraulic energy to move slurries. This design supports continuous flow, even when dealing with high concentrations of solids.
Several characteristics make a centrifugal slurry pump particularly well-suited to mining:
- Impeller Geometry: Specialized designs minimize particle collision and turbulence, reducing component erosion.
- Wear-Resistant Liners and Alloys: Materials like high-chrome white iron and elastomeric linings extend service life under harsh conditions.
- Energy Transfer Efficiency: These pumps are often designed to maximize output while minimizing energy loss, which becomes critical in operations dealing with highly viscous or chemically reactive slurries.
The result? Lower wear rates, improved flow assurance, and greater resilience under variable loads.
Operational Benefits Observed in Mining Companies Using These Pumps
For procurement leads and operations teams evaluating pump systems, performance metrics drive decision-making. In mining operations that have adopted centrifugal slurry pumps, the following benefits are frequently observed:
- Extended Maintenance Intervals: Reduced need for service translates to fewer interruptions in production schedules.
- Higher Uptime Metrics: Consistent performance under abrasive conditions contributes directly to meeting output targets.
- Adaptive Performance: These pumps handle variable load and solids content more efficiently, accommodating fluctuations in feedstock composition or operational stress.
Moreover, integrating centrifugal slurry pumps with SCADA and other monitoring systems enhances predictive maintenance, enabling early detection of performance issues and minimizing costly breakdowns.
Strategic Considerations When Evaluating a Slurry Pump Solution
From a business perspective, the price tag of a pump only tells part of the story. Lifecycle costs—including maintenance, energy use, and replacement frequency—paint a fuller picture. Organizations evaluating a centrifugal slurry pump in mining should consider the following:
- Total Cost of Ownership (TCO): Although initial costs may be higher, reduced failure rates and lower maintenance frequency can lead to long-term savings.
- Vendor Evaluation Frameworks: Proven performance in similar abrasive applications, availability of field support, and compatibility with remote monitoring platforms are all critical factors.
- Automation and Integration: Ensuring the pump integrates seamlessly with existing SCADA, predictive analytics, or IoT frameworks can improve both performance and oversight.
[ILLUSTRATIVE EXAMPLE]
In a generalized procurement scenario, a mid-sized mining firm adjusted its vendor evaluation criteria to emphasize past MTBF performance, SCADA integration capability, and metallurgical quality. By aligning vendor selection with these benchmarks, the resulting centrifugal slurry pump deployment contributed to a noticeable improvement in equipment uptime over a 12-month period.
[END EXAMPLE]
Key Metrics to Watch When Implementing Centrifugal Slurry Pumps
To effectively gauge the value of pump upgrades, operations managers should track metrics that reflect both system health and operational efficiency. Key performance indicators include:
- Mean Time Between Failures (MTBF): Increased MTBF indicates less frequent repairs and improved reliability.
- Slurry Throughput Efficiency: Flow consistency and pressure maintenance signal effective solids transport.
- Safety and Environmental Compliance: Equipment that contains slurry effectively reduces spill risks and aligns with regulatory standards.
By aligning pump performance with these metrics, mining companies can make informed decisions that support both compliance and profitability.
Conclusion
Centrifugal slurry pumps offer tangible performance advantages for mining operations handling abrasive fluids. By improving uptime, reducing maintenance frequency, and lowering long-term operational costs, these pumps contribute directly to better ROI and regulatory assurance. For stakeholders managing procurement and performance under intense operational pressure, reevaluating current pump systems against centrifugal slurry pump alternatives may be a worthwhile consideration.
Frequently Asked Questions (FAQs)
Q: What factors most impact ROI when investing in centrifugal slurry pumps?
A: ROI typically hinges on extended pump life, decreased downtime, reduced maintenance costs, and improved slurry containment. Evaluating lifecycle cost instead of initial purchase price offers a clearer view of financial impact.
Q: How do these pumps integrate with modern SCADA systems in mining operations?
A: Most industrial-grade centrifugal slurry pumps can be equipped with sensors and communication modules, allowing them to feed operational data into SCADA platforms for real-time monitoring and maintenance planning.
Q: What operational practices help maximize pump lifespan in abrasive conditions?
A: Regular inspection schedules, using wear-resistant materials, and proper pump sizing are among the most widely accepted practices. Integration with predictive maintenance tools also supports longer service life.
Frequently Unasked Questions (FUQs)
Q: How does improper pump sizing quietly erode operational margins over time?
A: A mismatched pump can lead to inefficient energy use, higher wear rates, and premature failure—often without triggering immediate alarms. Over time, this silent erosion reduces throughput and inflates maintenance costs.
Q: What are the hidden regulatory risks of using pumps with suboptimal containment in abrasive slurry environments?
A: Inadequate containment can increase the likelihood of slurry spills, which may lead to environmental penalties or safety violations under regulations like those enforced by the EPA.
Q: How do inconsistent maintenance protocols create cumulative reliability issues for centrifugal pumps?
A: Irregular maintenance can lead to minor damages compounding into major failures, particularly in high-abrasion contexts. This compromises MTBF metrics and increases operational risk.
Leave a Reply