Understanding Centrifugal Slurry Pumps: An In-Depth Guide
If you work in mining, construction, or manufacturing, you’ve probably heard of the centrifugal slurry pump. It’s a powerhouse that keeps operations running smoothly by handling the tough job of moving dense and abrasive slurries. But how exactly do these pumps work, and why are they so essential in industrial settings? In this guide, we’ll dive into the mechanics, applications, and maintenance of centrifugal slurry pumps, helping you make informed decisions to optimize performance and reduce downtime.
How Do Centrifugal Slurry Pumps Work?
At their core, centrifugal slurry pumps operate on a simple yet effective principle. The pump uses a rotating impeller to impart energy to the slurry, which is a mixture of water and solid particles. This energy conversion pushes the slurry through the pump and out into a discharge system, directing it where it’s needed. Let’s break down the components that make this happen:
- Impeller: The heart of the pump, the impeller spins rapidly, creating centrifugal force that drives the slurry outward. Depending on the type of slurry and the application, impellers can vary in design—open, semi-open, or enclosed.
- Casing: Surrounding the impeller, the casing collects and directs the slurry flow. It’s typically designed in a spiral shape (volute) to efficiently guide the slurry out of the pump. The casing material is crucial because it must withstand the abrasive nature of slurries.
- Shaft and Bearings: These components support and stabilize the impeller as it rotates. Maintaining the shaft’s alignment and the bearings’ integrity is key to preventing costly failures.
- Seal: The seal prevents leakage, a common challenge when handling abrasive materials. Different types of seals—such as mechanical seals, expeller seals, or packed gland seals—are used based on the application requirements and slurry characteristics.
By understanding each part’s role, you gain insight into how centrifugal slurry pumps handle abrasive and dense materials effectively. But their functionality doesn’t stop there. The versatility of these pumps makes them invaluable across several industries.
Applications of Centrifugal Slurry Pumps
Centrifugal slurry pumps are workhorses in industrial settings where moving slurries is a daily task. Here are some common applications:
1. Mining Industry
In mining, the centrifugal slurry pump is essential for transporting slurry mixtures that contain rocks, minerals, and water. Whether it’s in the extraction process or transporting tailings, these pumps ensure the efficient movement of dense slurries. The heavy-duty construction and material adaptability make them perfect for this abrasive and high-wear environment.
2. Construction Sector
In construction, these pumps manage everything from moving wet concrete mixtures to transporting slurries from drilling operations. Construction sites often present challenging conditions, such as variable flow rates and rough mixtures. Centrifugal slurry pumps are designed to handle these changes without compromising performance.
3. Manufacturing Processes
Centrifugal slurry pumps assist in various manufacturing processes, including chemical processing, food processing, and the pulp and paper industry. In these sectors, pumps are used to handle liquid-solid mixtures like chemicals, food by-products, or pulp. Their ability to manage different viscosities and abrasiveness levels makes them ideal for such diverse environments.
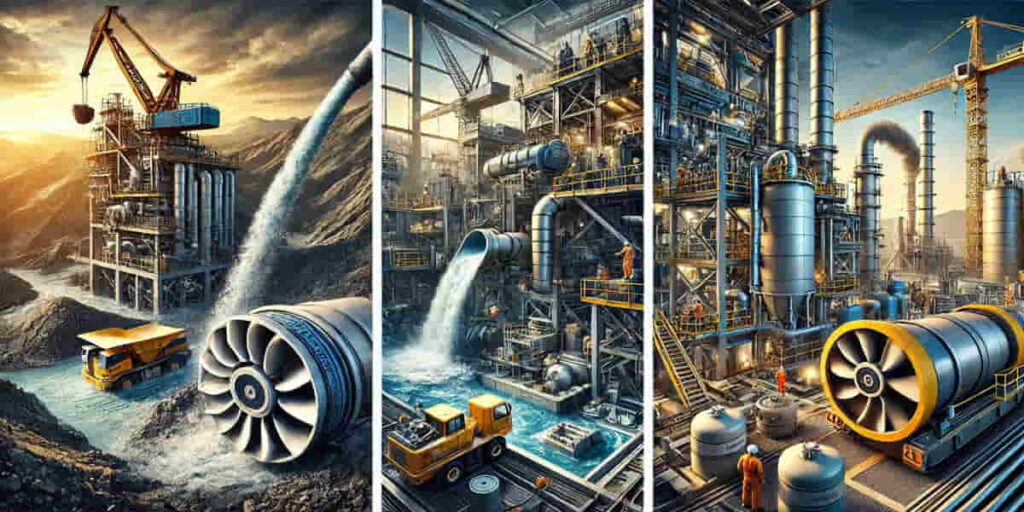
Types of Centrifugal Slurry Pumps
Not all centrifugal slurry pumps are built the same. Choosing the right type is critical for ensuring efficiency and longevity. Let’s explore the most common types:
- Rubber-Lined vs. Metal-Lined: Rubber-lined pumps are excellent for handling smaller, softer particles, as the rubber provides better wear resistance in such conditions. Metal-lined pumps, on the other hand, are more suitable for coarse, sharp, and large particles, offering greater durability under extreme conditions.
- Horizontal vs. Vertical Pumps: Horizontal pumps are the most commonly used in industrial applications due to their versatility and ease of installation. Vertical pumps, however, are beneficial when space is limited or when dealing with deep sumps or pits, as their design allows for the motor to be positioned above the fluid level, reducing risk and improving accessibility.
Each type has its own advantages, and the choice depends on the specific application, slurry characteristics, and operational environment. Selecting the right centrifugal slurry pump type ensures you get the best performance while minimizing wear and tear.
Cavitation: What It Is and How to Prevent It
Cavitation is a common issue in centrifugal slurry pumps that occurs when air bubbles form and collapse within the pump. This can lead to significant damage to the impeller and other components, reducing efficiency and increasing maintenance needs. Cavitation usually happens when there is insufficient pressure at the pump’s inlet, leading to vapor formation.
How to Prevent Cavitation:
- Maintain Proper Inlet Pressure: Ensure the pump is receiving adequate pressure at the inlet to prevent the formation of vapor bubbles.
- Optimize Pump Speed: Operating the pump at its optimal speed helps maintain consistent pressure and reduces the risk of cavitation.
- Use Appropriate Pump Design: Choosing the right pump design and size for the specific slurry and flow conditions can minimize the likelihood of cavitation, protecting your equipment and ensuring smooth operations.
Maintenance and Efficiency Tips
Let’s be honest—slurry pumps undergo significant stress. Handling abrasive materials day in and day out means that regular maintenance is non-negotiable if you want to avoid unplanned downtime and extend pump life. Here are some best practices for maintaining centrifugal slurry pumps:
- Regular Inspection: Inspect the pump components, especially the impeller, casing, and seals, for wear and tear. Catching issues early can save both time and money.
- Seal Maintenance: The seal is one of the most vulnerable parts of a slurry pump. Depending on the seal type, ensure that it’s properly lubricated and inspect it for leaks or damage. If left unchecked, a worn seal can lead to catastrophic failures.
- Impeller Adjustment: The impeller clearance should be adjusted periodically. Too much clearance can reduce pump efficiency, while too little can cause damage. Consult the manufacturer’s guidelines for specific measurements and maintenance intervals.
- Bearing Lubrication: Bearings are critical for smooth pump operation. Follow a strict lubrication schedule to prevent overheating or seizing, which can lead to significant downtime and repair costs.
- Monitor Pump Performance: Use monitoring equipment to track flow rates, pressure, and vibrations. Sudden changes in these metrics could signal a problem, allowing you to take action before a failure occurs.
By implementing these maintenance tips, you’ll not only keep your pump running efficiently but also extend its service life, optimizing your overall operational efficiency.
Conclusion: Making the Most of Centrifugal Slurry Pumps
Centrifugal slurry pumps are indispensable in many industries, from mining to construction and specific manufacturing sectors like chemical processing, food processing, and pulp and paper. Understanding their mechanics, choosing the right type for your specific application, and following a consistent maintenance schedule can significantly impact your operations’ efficiency and cost-effectiveness.
Next time you’re evaluating your slurry pumping needs, remember the key to maximizing performance lies in understanding the specifics: the type of pump, its components, and proper maintenance routines. When managed correctly, these pumps will reward your business with reliability and long-term efficiency, ensuring that you stay ahead in even the toughest industrial environments.